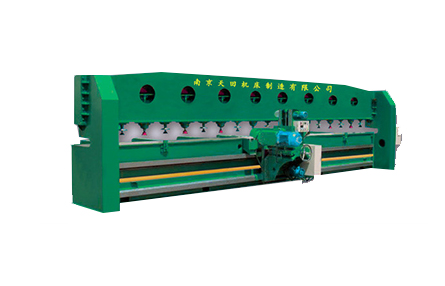
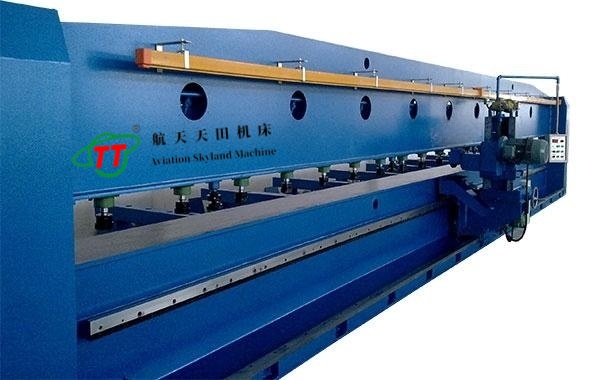
本文詳細(xì)探討單頭通用銑邊機(jī)的應(yīng)用場地、核心作用及性能特點(diǎn)。通過分析其在廣泛適用于鍋爐、壓力容器制造行業(yè)、造船、電力、石油、化工機(jī)械、工程機(jī)械制造,對各類低碳鋼板、不銹鋼板及鋁板在焊接前的坡口加工、斜邊、直邊、U型坡口能一次銑削成型,等行業(yè)的應(yīng)用場景,闡述其在材料邊緣處理中的關(guān)鍵作用;并從設(shè)備結(jié)構(gòu)、加工能力、操作便利性等維度深入剖析性能特點(diǎn),為相關(guān)企業(yè)合理選擇與高效使用該設(shè)備提供參考依據(jù),助力提升生產(chǎn)效率與加工質(zhì)量;與刨邊機(jī)相比,具有價(jià)格低、能耗低、工效高、光潔度高、操作及維修方便等優(yōu)點(diǎn)。
單頭通用銑邊機(jī);應(yīng)用場地;作用;性能特點(diǎn)
在現(xiàn)代工業(yè)生產(chǎn)中,材料邊緣的加工質(zhì)量對產(chǎn)品的整體性能與裝配精度有著直接影響。單頭通用銑邊機(jī)作為一種常見的邊緣加工設(shè)備,憑借其靈活性與通用性,在眾多工業(yè)領(lǐng)域發(fā)揮著重要作用。深入了解其應(yīng)用場地、作用及性能特點(diǎn),有助于企業(yè)根據(jù)自身生產(chǎn)需求合理配置設(shè)備,優(yōu)化生產(chǎn)流程,提升產(chǎn)品競爭力 。
在金屬板材與型材加工中,單頭通用銑邊機(jī)應(yīng)用廣泛。對于鋼板加工企業(yè),在生產(chǎn)各類金屬構(gòu)件時(shí),需對鋼板邊緣進(jìn)行處理,如切割后的鋼板邊緣存在毛刺、氧化皮等缺陷,單頭通用銑邊機(jī)可將其去除,使邊緣平整光滑,為后續(xù)焊接、折彎等工序做好準(zhǔn)備。在不銹鋼制品加工中,無論是廚具、裝飾部件還是工業(yè)設(shè)備零件,通過銑邊機(jī)加工邊緣,可提高產(chǎn)品的美觀度與精度 。
機(jī)械零部件制造過程中,許多零件的邊緣需要精確加工。單頭通用銑邊機(jī)可用于齒輪、法蘭、軸類等零件的邊緣銑削,去除加工余量,保證零件的尺寸精度與表面質(zhì)量,滿足裝配要求。例如,在減速機(jī)制造中,箱體的邊緣加工直接影響密封性能,銑邊機(jī)能夠精準(zhǔn)加工出符合標(biāo)準(zhǔn)的邊緣,確保設(shè)備運(yùn)行時(shí)無泄漏 。
鋼結(jié)構(gòu)建筑的建設(shè)離不開大量鋼材的加工。單頭通用銑邊機(jī)可對鋼梁、鋼柱等構(gòu)件的邊緣進(jìn)行加工,制作焊接坡口,提高焊接質(zhì)量與結(jié)構(gòu)穩(wěn)定性。在橋梁建設(shè)中,鋼梁的拼接需要高精度的邊緣加工,銑邊機(jī)能夠保證坡口角度與尺寸的一致性,增強(qiáng)橋梁結(jié)構(gòu)的承載能力 。
壓力容器的安全性要求極高,對材料邊緣加工精度把控嚴(yán)格。單頭通用銑邊機(jī)可對壓力容器用鋼板進(jìn)行銑邊處理,去除表面缺陷,加工出合適的焊接坡口,確保焊接接頭強(qiáng)度,滿足壓力容器的制造標(biāo)準(zhǔn) 。
有效去除材料在前期加工(如切割、鍛造)中產(chǎn)生的毛刺、毛邊、熔渣及不平整部分,使材料邊緣達(dá)到平滑、規(guī)整的狀態(tài),避免在后續(xù)加工或使用過程中劃傷操作人員或影響其他部件的裝配 。
根據(jù)不同焊接工藝需求,加工出各類形狀與角度的焊接坡口,如 V 形、U 形、X 形等。合理的坡口設(shè)計(jì)能增加焊縫熔合面積,提高焊接質(zhì)量,減少焊接變形與缺陷,確保焊接接頭的強(qiáng)度與可靠性 。
通過精確的定位與進(jìn)給系統(tǒng),保證材料邊緣的加工尺寸符合設(shè)計(jì)圖紙要求,將尺寸誤差控制在極小范圍內(nèi)。對于一些對精度要求較高的零件,銑邊機(jī)可通過多次銑削逐步達(dá)到規(guī)定尺寸,滿足高精度加工需求 。
通過銑削加工,降低材料邊緣的表面粗糙度,提高表面光潔度,改善材料的外觀質(zhì)量。對于一些外觀要求較高的產(chǎn)品,良好的表面質(zhì)量有助于提升產(chǎn)品的市場競爭力 。
單頭通用銑邊機(jī)結(jié)構(gòu)設(shè)計(jì)簡潔,占地面積小,適用于各類規(guī)模的生產(chǎn)車間。其可通過更換不同規(guī)格的刀具、調(diào)整加工參數(shù),適應(yīng)多種材料(如碳鋼、不銹鋼、合金鋼等)與不同形狀、尺寸的工件加工,滿足多樣化生產(chǎn)需求,尤其適合小批量、多品種的加工場景 。
設(shè)備配備直觀的操作界面與控制面板,操作人員經(jīng)過簡單培訓(xùn)即可熟練掌握操作方法。其機(jī)械結(jié)構(gòu)與控制系統(tǒng)相對簡單,零部件布局合理,日常的檢查、保養(yǎng)與維修工作便捷。刀具更換流程簡單,可快速完成,減少停機(jī)時(shí)間,提高設(shè)備利用率 。
采用精密的導(dǎo)軌、絲桿等傳動部件,配合高精度的定位系統(tǒng),能夠保證銑削加工的精度。在加工過程中,通過穩(wěn)定的進(jìn)給速度與刀具轉(zhuǎn)速控制,可有效減少加工誤差,實(shí)現(xiàn)平面度、直線度、垂直度等指標(biāo)的高精度加工,滿足一般工業(yè)生產(chǎn)對零件精度的要求 。
雖然單頭銑邊機(jī)相比雙頭或多頭銑邊機(jī)在加工效率上稍顯遜色,但對于中小批量生產(chǎn)任務(wù),其加工效率能夠滿足需求。同時(shí),通過優(yōu)化加工工藝與合理安排生產(chǎn)計(jì)劃,可進(jìn)一步提高生產(chǎn)效率。此外,單頭銑邊機(jī)的能耗相對較低,運(yùn)行成本較為經(jīng)濟(jì) 。
設(shè)備設(shè)置了完善的安全防護(hù)裝置,如防護(hù)罩、急停按鈕、過載保護(hù)等,可有效防止操作人員受到意外傷害,保障設(shè)備的安全穩(wěn)定運(yùn)行。在設(shè)計(jì)上充分考慮人機(jī)工程學(xué)原理,降低操作人員的勞動強(qiáng)度與疲勞感。
This paper thoroughly explores the application sites, core functions, and performance characteristics of single-head universal edge milling machines. By analyzing their application scenarios in industries such as boiler and pressure vessel manufacturing, shipbuilding, electric power, petroleum, chemical machinery, and construction machinery manufacturing, where they are widely used for the groove processing of various low-carbon steel plates, stainless steel plates, and aluminum plates before welding, and can achieve one-time milling forming for bevel edges, straight edges, and U-shaped grooves, etc., this paper expounds their crucial role in material edge processing. It also deeply analyzes the performance characteristics from dimensions such as equipment structure, processing capacity, and operation convenience, providing a reference basis for relevant enterprises to reasonably select and efficiently use this equipment, helping to improve production efficiency and processing quality. Compared with edge planers, it has the advantages of lower price, lower energy consumption, higher efficiency, higher finish, and convenient operation and maintenance.
Single-head universal edge milling machine; Application sites; Functions; Performance characteristics
In modern industrial production, the processing quality of material edges directly affects the overall performance and assembly accuracy of products. As a common edge processing equipment, the single-head universal edge milling machine plays an important role in many industrial fields due to its flexibility and versatility. A deep understanding of its application sites, functions, and performance characteristics helps enterprises to reasonably allocate equipment according to their own production needs, optimize production processes, and enhance product competitiveness.
Single-head universal edge milling machines are widely used in the processing of metal plates and profiles. For steel plate processing enterprises, when producing various metal components, the edges of steel plates need to be processed. For example, there are defects such as burrs and oxide scales on the edges of steel plates after cutting. Single-head universal edge milling machines can remove these defects, making the edges flat and smooth, and preparing for subsequent processes such as welding and bending. In the processing of stainless steel products, whether it is kitchenware, decorative parts, or industrial equipment parts, processing the edges with an edge milling machine can improve the appearance and precision of the products.
During the manufacturing process of mechanical parts, the edges of many parts require precise processing. Single-head universal edge milling machines can be used for the edge milling of parts such as gears, flanges, and shafts, removing machining allowances, ensuring the dimensional accuracy and surface quality of parts, and meeting assembly requirements. For example, in the manufacturing of reducers, the edge processing of the casing directly affects the sealing performance. The edge milling machine can precisely process edges that meet the standards, ensuring no leakage during the operation of the equipment.
The construction of steel structure buildings is inseparable from the processing of a large amount of steel. Single-head universal edge milling machines can process the edges of components such as steel beams and columns, fabricate welding grooves, and improve the welding quality and structural stability. In bridge construction, the splicing of steel beams requires high-precision edge processing. The edge milling machine can ensure the consistency of groove angles and dimensions, enhancing the load-bearing capacity of the bridge structure.
The safety requirements of pressure vessels are extremely high, and strict control is required for the processing accuracy of material edges. Single-head universal edge milling machines can mill the edges of steel plates used for pressure vessels, remove surface defects, and process appropriate welding grooves to ensure the strength of welding joints and meet the manufacturing standards of pressure vessels.
Effectively remove burrs, rough edges, slag, and uneven parts generated during previous processing (such as cutting and forging) of materials, making the material edges smooth and regular, avoiding scratching operators or affecting the assembly of other components during subsequent processing or use.
According to different welding process requirements, various shapes and angles of welding grooves such as V-shaped, U-shaped, and X-shaped can be processed. A reasonable groove design can increase the fusion area of the weld, improve the welding quality, reduce welding deformation and defects, and ensure the strength and reliability of the welding joint.
Through a precise positioning and feeding system, ensure that the processed dimensions of the material edges meet the requirements of the design drawings, and control the dimensional error within a very small range. For some parts with high precision requirements, the edge milling machine can gradually reach the specified dimensions through multiple milling operations to meet the requirements of high-precision processing.
Through milling processing, reduce the surface roughness of the material edges, improve the surface finish, and enhance the appearance quality of the materials. For products with high appearance requirements, good surface quality helps to enhance the market competitiveness of the products.
The single-head universal edge milling machine has a simple structural design and occupies a small area, making it suitable for production workshops of various scales. It can adapt to the processing of various materials (such as carbon steel, stainless steel, alloy steel, etc.) and workpieces of different shapes and sizes by replacing tools of different specifications and adjusting processing parameters, meeting diversified production needs, especially suitable for small-batch and multi-variety processing scenarios.
The equipment is equipped with an intuitive operation interface and control panel, and operators can master the operation method proficiently after simple training. Its mechanical structure and control system are relatively simple, with a reasonable layout of components, facilitating daily inspection, maintenance, and repair work. The tool replacement process is simple and can be completed quickly, reducing downtime and improving equipment utilization.
Precision guide rails, lead screws and other transmission components are used, combined with a high-precision positioning system, which can ensure the precision of milling processing. During the processing, through the control of stable feed speed and tool rotation speed, processing errors can be effectively reduced, and high-precision processing of indicators such as flatness, straightness, and perpendicularity can be achieved to meet the precision requirements of parts in general industrial production.
Although the processing efficiency of single-head edge milling machines is slightly inferior to that of double-head or multi-head edge milling machines, for small and medium batch production tasks, their processing efficiency can meet the requirements. At the same time, the production efficiency can be further improved by optimizing the processing technology and reasonably arranging the production plan. In addition, single-head edge milling machines have relatively low energy consumption and economical operation costs.
The equipment is equipped with a complete set of safety protection devices, such as protective covers, emergency stop buttons, and overload protection, which can effectively prevent operators from accidental injuries and ensure the safe and stable operation of the equipment. The ergonomic principles are fully considered in the design to reduce the labor intensity and fatigue of operators
五、XBJ-C系列單頭銑邊機(jī)技術(shù)參數(shù)(echnical Parameters of Single-head Edge Milling Machine):
序號NO | 項(xiàng)目 | 相關(guān)技術(shù)參數(shù) |
1 | 有效銑削長度(mm) | 4000 | 6000 | 9000 | 12000 | 14000 | 16000 | 18000 |
2 | 加工鋼板厚度(mm) | 6-140(也可根據(jù)用戶訂制) |
3 | 銑削角度(°) | 0-45 可訂制0-90 |
4 | 快進(jìn)快退速度(mm) | 0-2200(采用變頻無極調(diào)速) |
5 | 銑削速度(mm/min) | O--1000mm(由板材材質(zhì)決定銑削速度) |
6 | 一次最大銑削斜邊寬度(mm) | 30mm |
7 | 升降電機(jī)功率(KW) | 0.55 |
8 | 加工表面粗糙度 | Ra3.2-6.3 |
9 | 銑削主軸轉(zhuǎn)速(mm/min) | 580轉(zhuǎn)(銑邊機(jī)專用銑頭)也可配置變頻調(diào)速 |
10 | 液壓壓料缸數(shù)(只) | 9 | 13 | 19 | 25 | 29 | 33 | 37 |
11 | 托料架只數(shù)(只) | 5 | 7 | 10 | 12 | 14 | 16 | 18 |
12 | 壓料臺距地面高度(mm) | 900 |
13 | 進(jìn)給電機(jī)功率(KW) | 1.5變頻調(diào)速(雙級擺線針輪減速機(jī)) |
14 | 銑削電機(jī)功率(KW) | 5.5(也可根據(jù)用戶要求配置) |
15 | 油泵電機(jī)功率(KW) | 5.5 |
16 | 液壓系統(tǒng)壓力(兆帕) | 3.5 |
|
|
|
|
|
|
|
|
|
|
|
|
本資料所列數(shù)據(jù)為參考數(shù)據(jù),如與機(jī)床實(shí)際數(shù)據(jù)不符,應(yīng)以機(jī)床實(shí)際數(shù)據(jù)為準(zhǔn),以上參數(shù)如有變動,恕不另行通知,本公司保留對此資料的最終解釋權(quán)!
The data listed in this material are for reference. In case of any discrepancy with the actual data of the machine tool, the actual data of the machine tool shall prevail.
Any changes to the above parameters will not be separately notified, and our company reserves the right to the final interpretation of this material!